1. 이론적 검증 및 분석
3개 중타이어 밸브회사에서 제공한 샘플 중 2개는 밸브이고 1개는 아직 사용되지 않은 밸브입니다.A와 B의 경우 사용되지 않은 밸브는 회색으로 표시되어 있습니다.포괄적인 그림 1.밸브 A의 외부 표면은 얕고, 밸브 B의 외부 표면은 표면이며, 밸브 C의 외부 표면은 표면이고, 밸브 C의 외부 표면은 표면입니다.밸브 A와 B는 부식 생성물로 덮여 있습니다.밸브 A와 B는 굽힘 부분에서 균열이 있고, 굽힘의 바깥쪽 부분은 밸브를 따라 있고, 밸브 링 마우스 B는 끝부분을 향해 균열이 있으며, 밸브 A 표면의 균열 표면 사이의 흰색 화살표가 표시되어 있습니다.위에서 보면 균열은 어디에나 있고, 균열이 가장 크고, 균열이 어디에나 있습니다.
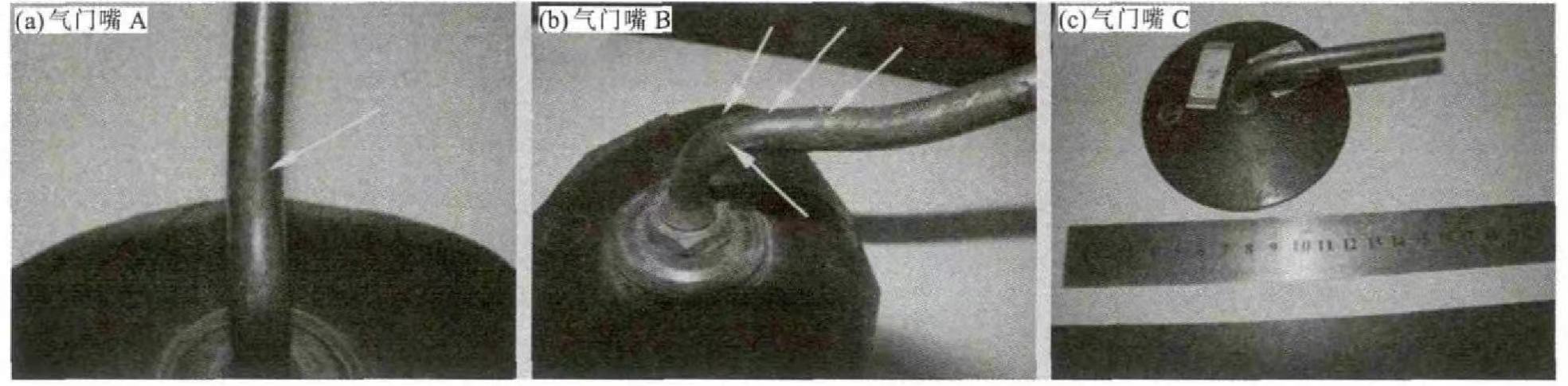
의 한 부분타이어 밸브A, B, C 시료를 굽힘부에서 잘라내어 ZEISS-SUPRA55 주사전자현미경으로 표면 형태를 관찰하고, EDS를 이용하여 미세면적 조성을 분석하였다. 그림 2(a)는 밸브 B 표면의 미세구조를 보여준다. 표면에는 흰색의 밝은 입자들이 많이 존재하며(그림의 흰색 화살표), EDS 분석 결과 황(S) 함량이 높은 것을 확인할 수 있다. 흰색 입자의 에너지 스펙트럼 분석 결과는 그림 2(b)에 나타내었다.
그림 2(c)와 (e)는 밸브 B의 표면 미세 구조입니다.그림 2(c)에서 볼 수 있듯이 표면은 거의 완전히 부식 생성물로 덮여 있으며 에너지 스펙트럼 분석에 의한 부식 생성물의 부식성 원소는 주로 S, Cl 및 O를 포함하고 각 위치에서 S의 함량이 더 높으며 에너지 스펙트럼 분석 결과는 그림 2(d)에 나와 있습니다.그림 2(e)에서 볼 수 있듯이 밸브 A의 표면에서 밸브 링을 따라 미세 균열이 있습니다.그림 2(f)와 (g)는 밸브 C의 표면 미세 형태이며 표면도 부식 생성물로 완전히 덮여 있으며 부식성 원소도 그림 2(e)와 유사하게 S, Cl 및 O를 포함합니다.균열의 원인은 밸브 표면의 부식 생성물 분석에서 응력 부식 균열(SCC)일 수 있습니다. 그림 2(h)는 밸브 C의 표면 미세구조를 보여줍니다. 표면이 비교적 깨끗한 것을 확인할 수 있으며, EDS 분석 결과 표면의 화학 조성이 구리 합금과 유사하여 밸브가 부식되지 않았음을 나타냅니다. 세 밸브 표면의 미세 형태와 화학 조성을 비교함으로써, 주변 환경에 S, O, Cl과 같은 부식성 매질이 존재함을 알 수 있습니다.
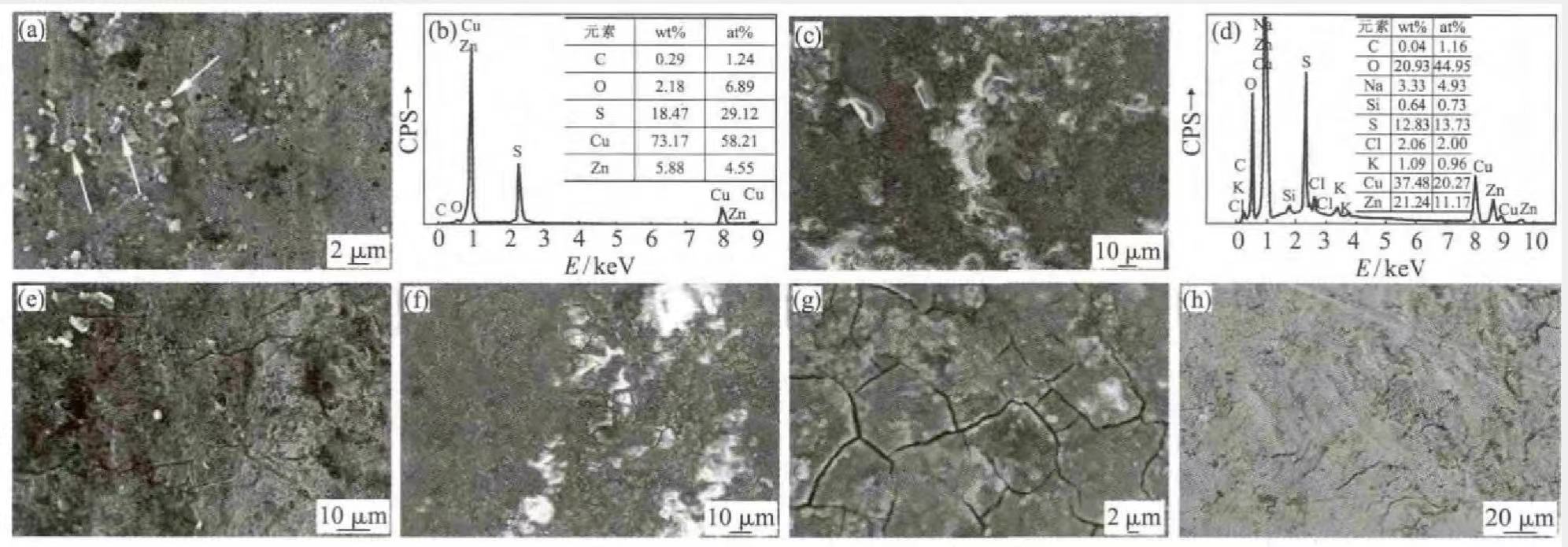
밸브 B의 균열은 굽힘 시험을 통해 개방되었으며, 균열이 밸브의 전체 단면을 관통하지 않고, 백벤드 측에서 균열이 발생했으며, 밸브 백벤드 반대쪽에는 균열이 발생하지 않은 것으로 확인되었습니다. 균열을 육안으로 검사한 결과, 균열의 색상이 어두워 균열이 부식되었음을 나타내며, 균열의 일부 영역은 색상이 어두워 부식이 이 부분에서 더 심각함을 나타냅니다. 밸브 B의 균열은 주사 전자 현미경으로 관찰되었으며, 그림 3과 같습니다. 그림 3(a)는 밸브 B 균열의 거시적 모습을 보여줍니다. 밸브 근처의 외부 균열이 부식 생성물로 덮여 있는 것을 볼 수 있으며, 이는 주변 환경에 부식성 매체가 존재함을 다시 한번 나타냅니다. 에너지 스펙트럼 분석에 따르면, 부식 생성물의 화학 성분은 주로 S, Cl, O이며, 그림 3(b)와 같이 S와 O의 함량이 비교적 높습니다. 균열 표면을 관찰한 결과, 균열 성장 패턴이 결정형을 따르는 것으로 나타났습니다. 그림 3(c)에서 볼 수 있듯이, 고배율로 파단면을 관찰하면 다수의 2차 균열을 확인할 수 있습니다. 2차 균열은 그림에서 흰색 화살표로 표시되어 있습니다. 파단면의 부식 생성물과 균열 성장 양상은 응력 부식 균열의 특성을 다시 한번 보여줍니다.
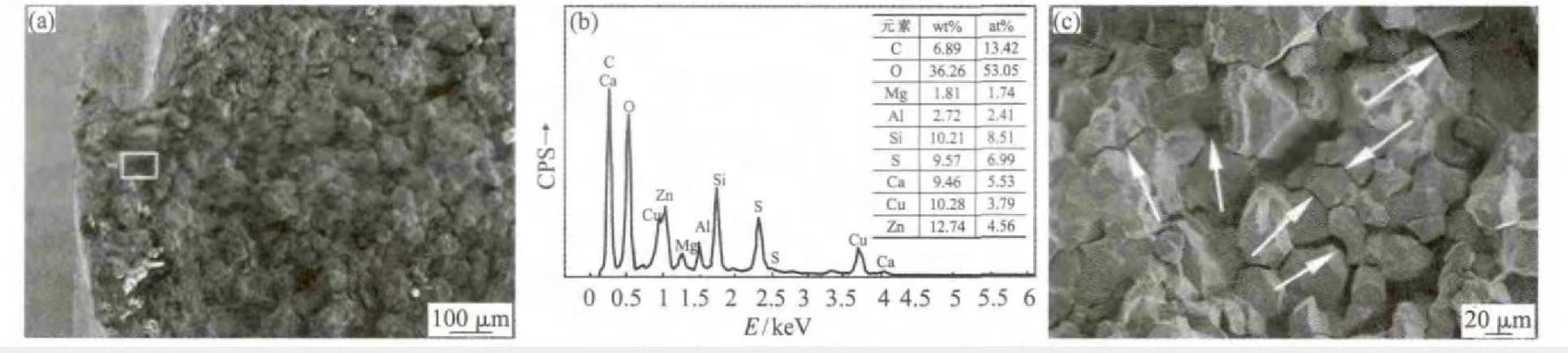
밸브 A의 균열은 열리지 않았고, 밸브의 일부(균열 위치 포함)를 제거하고, 밸브의 축 단면을 연삭 및 연마한 후 FeCl3(5g) + HCl(50mL) + C2H5OH(100mL) 용액을 사용하여 에칭하고, Zeiss Axio Observer A1m 광학 현미경으로 금속 조직과 균열 성장 형태를 관찰했습니다.그림 4(a)는 밸브의 금속 조직을 보여주는데, α+β 이중상 구조이고, β는 비교적 미세하고 입상이며 α상 매트릭스에 분포합니다.원주 균열의 균열 전파 패턴은 그림 4(a), (b)에 나와 있습니다.균열 표면은 부식 생성물로 채워져 있기 때문에 두 균열 표면 사이의 틈이 넓어 균열 전파 패턴을 구분하기 어렵습니다.분기 현상. 이 1차 균열에서도 많은 2차 균열(그림에서 흰색 화살표로 표시)이 관찰되었고, 그림 4(c)를 참조하고, 이러한 2차 균열은 결정립을 따라 전파되었습니다. 에칭된 밸브 샘플을 SEM으로 관찰한 결과, 주 균열과 평행한 다른 위치에 많은 미세 균열이 있는 것으로 밝혀졌습니다. 이러한 미세 균열은 표면에서 발생하여 밸브 내부로 확장되었습니다. 균열은 분기되어 결정립을 따라 확장되었습니다. 그림 4(c), (d)를 참조하십시오. 이러한 미세 균열의 환경 및 응력 상태는 주 균열과 거의 동일하므로 주 균열의 전파 형태도 입계임을 추론할 수 있으며, 이는 밸브 B의 파괴 관찰을 통해서도 확인됩니다. 균열의 분기 현상은 다시 밸브의 응력 부식 균열의 특성을 보여줍니다.
2. 분석 및 논의
요약하자면, 밸브 손상은 SO2에 의한 응력 부식 균열로 인해 발생한다고 추론할 수 있습니다. 응력 부식 균열은 일반적으로 세 가지 조건을 충족해야 합니다. (1) 응력 부식에 민감한 재료, (2) 구리 합금에 민감한 부식성 매질, (3) 특정 응력 조건.
일반적으로 순수 금속은 응력 부식을 겪지 않으며 모든 합금은 다양한 정도로 응력 부식에 취약하다고 믿어집니다.황동 재료의 경우 일반적으로 이중상 구조가 단일상 구조보다 응력 부식 감수성이 더 높다고 믿어집니다.황동 재료의 Zn 함량이 20%를 초과하면 응력 부식 감수성이 더 높고 Zn 함량이 높을수록 응력 부식 감수성이 더 높다고 문헌에 보고되었습니다.이 경우 가스 노즐의 금속 조직은 α+β 이중상 합금이며 Zn 함량은 약 35%로 20%를 훨씬 초과하므로 응력 부식 감수성이 높고 응력 부식 균열에 필요한 재료 조건을 충족합니다.
황동 소재의 경우, 냉간 가공 변형 후 응력 제거 어닐링을 수행하지 않으면 적절한 응력 조건 및 부식 환경에서 응력 부식이 발생합니다. 응력 부식 균열을 유발하는 응력은 일반적으로 국부 인장 응력이며, 이는 작용 응력 또는 잔류 응력일 수 있습니다. 트럭 타이어에 공기가 주입된 후, 타이어 내부의 높은 압력으로 인해 공기 노즐의 축 방향을 따라 인장 응력이 발생하여 공기 노즐에 원주 방향 균열이 발생합니다. 타이어 내부 압력에 의한 인장 응력은 σ=p R/2t (여기서 p는 타이어 내부 압력, R은 밸브 내경, t는 밸브 벽 두께)로 간단히 계산할 수 있습니다. 그러나 일반적으로 타이어 내부 압력에 의해 발생하는 인장 응력은 크지 않으므로 잔류 응력의 영향을 고려해야 합니다. 가스 노즐의 균열 위치는 모두 백벤드(backbend)에 있으며, 백벤드 부분의 잔류 변형이 크고 잔류 인장 응력이 존재한다는 것은 명백합니다. 실제로 많은 실용적인 구리 합금 부품에서 응력 부식 균열은 설계 응력에 의해 발생하는 경우가 드물며, 대부분은 눈에 보이지 않고 무시되는 잔류 응력에 의해 발생합니다. 이 경우, 밸브의 뒤쪽 굽힘 부분에서 타이어 내부 압력에 의해 발생하는 인장 응력의 방향은 잔류 응력의 방향과 일치하며, 이 두 응력의 중첩이 SCC의 응력 조건을 제공합니다.
게시 시간: 2022년 9월 23일